DuPont Protection Solutions assure la protection des employés de Malteurop, leader mondial de la malterie
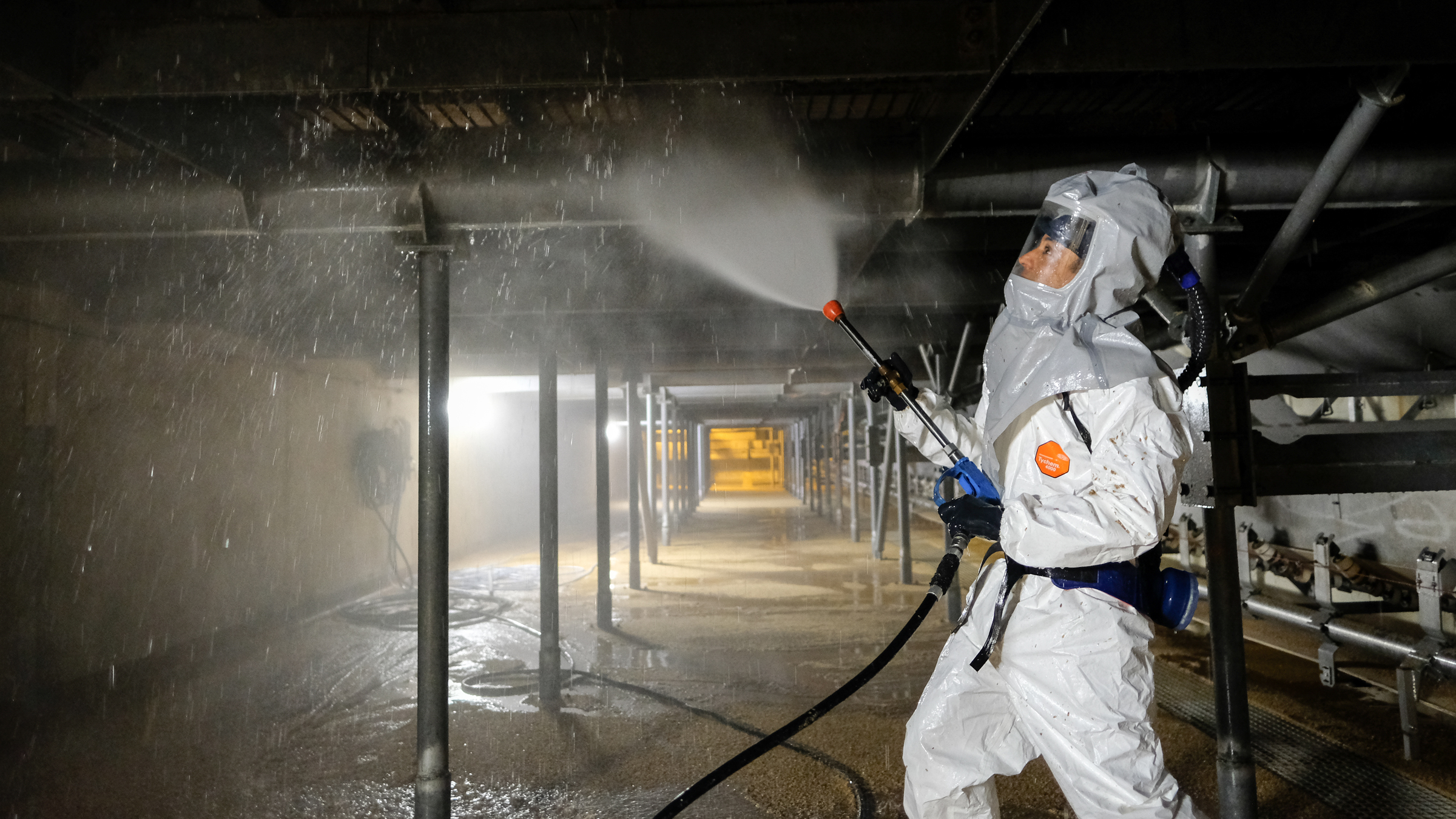
Fondé en 1984, le groupe Malteurop est l’un des premiers malteurs mondiaux. Née du regroupement d’un ensemble de coopératives, cette entreprise française transforme l’orge en malt qui sera ensuite utilisé par les brasseurs pour la fabrication de la bière. Avec 27 usines dans le monde réparties sur 4 continents où travaillent près de 1200 collaborateurs, Malteurop se positionne comme le premier intégrateur de la filière orge-malt-bière.
En France, le groupe compte 4 sites de production implantés au cœur du bassin céréalier, parmi lesquels la plus grosse usine Malteurop dans le monde : celle de Vitry-le-François d’une capacité de production de 240.000 tonnes par an. Pour cette industrie agro-alimentaire dont l’activité et l’environnement industriel présentent des risques spécifiques, la sécurité est une priorité absolue. Cette préoccupation de tous les instants a conduit Malteurop à s’entourer de l’expertise de DuPont Protection Solutions pour les accompagner dans leur choix du vêtement de protection haute performance le plus adapté à la formation de ses équipes.
Un process de fabrication maîtrisé au service de la qualité
Idéalement situé dans la 4ème ville du département de la Marne, à la convergence d’un nœud fluvial, autoroutier et ferroviaire, le site Malteurop de Vitry-le-François produit le malt qui servira à la fabrication de la bière blonde par ses clients brasseurs. Certifiée ISO 22000 (sécurité des denrées alimentaires), GMP+ (nutrition animale) et ISO 9001, l’usine dispose de 3 unités de fabrication où 65 personnes veillent 24 heures sur 24, 365 jours par an, au bon déroulement du processus de maltage.
La fabrication du malt suit ainsi un cheminement précis. Arrivé à 10-12 % d’humidité, l’orge subit différentes étapes de transformation avant stockage et expédition vers les brasseurs :
• après nettoyage, le grain est immergé dans une cuve de trempe. Ce procédé réveille et stimule le grain qui commence alors à germer,
• sorti de la trempe à 42% d’humidité, le grain reste ensuite dans un germoir pendant 4 à 5 jours à température ambiante (12-20°). Reposant sur des plateaux perforés munis d’un système de ventilation, le grain est remué toutes les 12 heures pour assurer son bon développement,
• vient ensuite le touraillage qui sèche le grain par paliers successifs de température jusqu’au coup de feu (80-85°). Cruciale, cette étape détermine la couleur de la future bière,
• après transfert dans des cellules de stockage intermédiaire, le produit passe dans la dégermeuse pour enlever les germes qui sont alors récupérés pour la fabrication de granulés destinés à l’alimentation animale.
Aussi bien en amont que tout au long du process de fabrication, l’orge et le malt font l’objet de toutes les attentions : test des nouvelles récoltes grâce à une micro-malterie qui permet d’ajuster les recettes de fabrication et contrôle qualité dans un laboratoire qui reproduit les conditions de fabrication de la bière. L’objectif : garantir un produit de qualité conforme aux cahiers des charges des clients brasseurs.
Pour Malteurop, la prévention des risques sanitaires alimentaires tout au long du processus de maltage constitue un véritable enjeu pour produire un malt sain. Un défi que l’industriel relève grâce à de bonnes pratiques de fabrication et à un processus de nettoyage complet systématique à chaque déchargement afin d’éviter tout risque microbiologique.
Une culture de la sécurité
Pour assurer les conditions d’hygiène et la sécurité alimentaire, le nettoyage est un souci quotidien chez Malteurop. Comme l’explique Denis Ricart, Animateur Prévention, « dans les germoirs et dans les cuves, il y a toujours une température entre 18 et 24 degrés et un taux d’humidité proche de 100%. Ce sont des conditions idéales pour le développement des bactéries, des moisissures et des champignons ». « C’est pourquoi dès qu’une cuve de trempe ou un germoir est vide, une équipe de nettoyage javellise l’enceinte, les dessous de germoir et les systèmes de transport du grain puis procède au rinçage à haute pression avant tout nouveau remplissage de l’installation », explique Véronique Coeffier, Assistante QHSE. « Ces opérations sont particulièrement essentielles au niveau des dessous de germoir où s’effectue la ventilation, pour éviter que les trous des plateaux ne soient bouchés par des grains d’orge car sans ventilation le grain s’asphyxie ».
A la malterie de Vitry-le-François, qui compte 12 germoirs et 2 cuves de trempes sur les unités M1 et M2 où le nettoyage est manuel, ces procédures rigoureuses sont consciencieusement effectuées une fois par jour. Jamel Bahri, employé depuis 6 ans chez Malteurop, est l’un des ouvriers de production qui réalise cette tache considérable au vu de la dimension des germoirs et du temps de nettoyage de chaque enceinte (entre 4 à 8 heures selon l’encrassement de la cuve). Revêtus de gants et d’une combinaison de protection chimique par dessus laquelle ils enfilent un heaume et un harnais avec ceinture de ventilation, les ouvriers ainsi exposés aux dangers liés à l’utilisation de la javel diluée avec fort risque de projection lors du rinçage à haute pression, subissent également de nombreuses contraintes posturales.
Sur un site comme celui de Malteurop avec des risques bien identifiés comme le risque ATEX (atmosphères explosives) et l’exposition aux produits chimiques, la sécurité est la première priorité de l’entreprise. Pour cette raison, Mélissa Chauvière, Responsable de Production, a fait appel à DuPont Protection Solutions afin de trouver ensemble des solutions visant à se rapprocher du risque zéro.
La sécurité des personnes : une priorité absolue
Pour répondre au plus près aux besoins de protection des opérateurs de production, DuPont Personal Protection s’est rendu sur le site de Vitry-le-François pour connaître avec précision les produits chimiques employés et constater les conditions réelles d’utilisation des combinaisons. Mélissa Chauvière de Malteurop souhaitait : « un vêtement qui soit facile à mettre, suffisamment résistant à la déchirure en cas d’accrochage » mais voulait « aussi une sensibilisation assez simple de son personnel à la bonne utilisation de la combinaison ».
Après plusieurs réunions de travail, DuPont Protection Solutions préconise la combinaison Tychem® 4000 S. Ce vêtement de catégorie III est tout particulièrement adapté pour ce type d’utilisation qui requiert une protection optimale contre les substances chimiques sans gêner les mouvements de l’utilisateur qui peut être amené à évoluer dans un espace réduit.
Des essais au porter sont alors effectués par les opérateurs selon les zones de nettoyage. A l’issue, la combinaison Tychem® 4000 S a été validée à l’unanimité par les ouvriers de production car comme l’indique Jamel Bahri « je me sens plus en sécurité, les coutures sont mieux protégées ». « Plus souple, plus ajustée au niveau du cou, plus légère et donc plus confortable à porter », « facile à enfiler, elle est dotée de manchettes qui tiennent beaucoup mieux grâce au passe-pouce élastiqué au poignet », « avec sa double fermeture à glissière et double rabat, elle est vraiment étanche, cela nous rassure » sont autant d’avis qui ont été recueillis par l’équipe sécurité de Malteurop.
La formation à la sécurité, un enjeu essentiel
Moyen privilégié d’améliorer la sécurité en permanence, la formation des équipes à l’habillage/nettoyage/ déshabillage était une autre demande de Malteurop qui, là encore, a apprécié « d’être accompagné à ce point par DuPont Protection Solutions tant dans le choix de la bonne combinaison, des tailles à commander que dans les bonnes pratiques à adopter » souligne Véronique Coeffier. Aujourd’hui, les procédures sont précises « avant d’utiliser tout produit chimique, le personnel, permanent comme intérimaire, suit une formation au préalable d’habillage/déshabillage. Chaque tache est décrite dans une fiche d’instruction qu’ils doivent lire avant de procéder à tout nettoyage » indique Mélissa Chauvière.
Et Véronique Coeffier de conclure : « cet accompagnement a été moteur dans la mise en place d’une approche globale de la sécurité et l’implication des équipes. Nous sommes vraiment satisfaits aujourd’hui de l’évolution positive que tout cela a eu ».
Pour plus d’informations, veuillez consulter le site www.fr.dupont.com/epi ou fr.dupont.com/safespec